
Revolutionary milestones in diamond manufacturing technology
Everything around us keeps upgrading continuously, from cell phones to wardrobes and even how we work. A big reason for this change is that technology keeps improving to make each task easier and more effortless. Thousands of studies are held regularly to solve every possible problem. This innovation not only affects our everyday chores but also how industries work. Technology can bring precision, excellence, and quality to different steps in the supply chain. Many small processes that used to be done by human hands are now quickly replaced by highly specialised machinery. All of these advancements also apply to the diamond industry, and immense development in this field's technological sector has led to a total revolution of the whole industry.

Everything from where diamonds are being mined to the level where they are processed and stored has changed because of technological advancements. Earlier, every tiny detail of a diamond at all stages was handcrafted by laborers. This is now replaced by the machinery of different capacities and functions. After the rough diamonds are sorted on the basis of shape, size, color, and quality, they are passed through a series of processes, including planning, marking, cleaving, bruting, and polishing. The introduction of technology has evolved how each of these processes is done.
Let's see how technology makes each process better.
Planning
Diamond planning is a stage where the raw diamond or a rough diamond is analysed to decide how to mark, cut, process, and use the diamond to get the best out of it without any wastage.
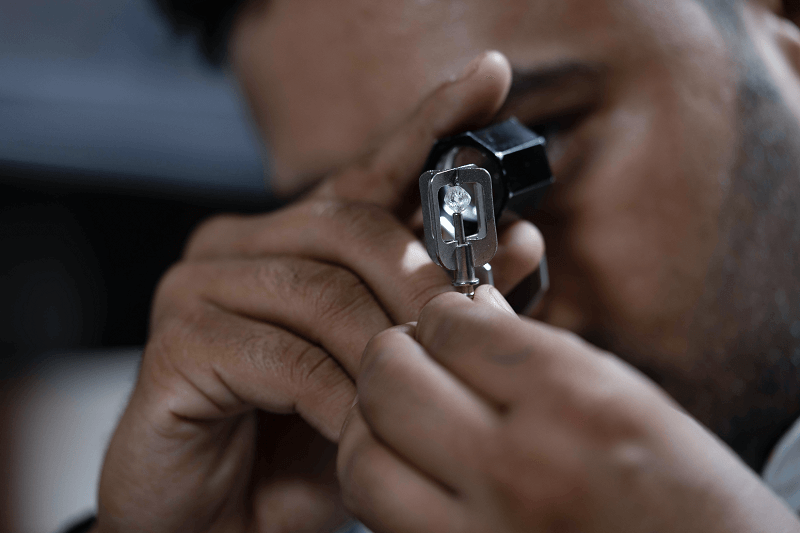
Planning was formerly done manually by skilled workers who would examine the rough diamond for impurities or defects. Depending on this, they planned to get the best part out of it in terms of weight and clarity and placed marks on it with a pen to guide the following process.
After the introduction of laser technology in the early 21st century, there was a drastic chang in the diamond industry. Laser technology can be used at every step in some way or the other. New technologies were invented that kept developing throughout the years.
The method in which the rough diamond is planned has also changed completely. The rough diamond is now measured on a 3D AI-assisted planning technology which guides the user to optimal yield from the diamond with laser mapping. It proposes a plan which shows how it can be converted into a finished diamond optimally and shows the weight, shape, and clarity of the supposed finished diamond. Minimizing the waste during the process and maximising a diamond's quality and value is the central motto of this step.
Marking
Marking is a process in which the best possible shape and cut of a diamond are outlined on the rough diamond. Traditionally, this was done by labourers using ink pens. Outlines were drawn at the locations where the diamond will be split.
A laser marking machine is used in which a very thin line is engraved on the diamond with a laser beam. This ensures finesse and precision and minimises mistakes. Because any minor flaws in the marking of the diamond, even small as the thread, can cause a significant change in the clarity grade of the final diamond.
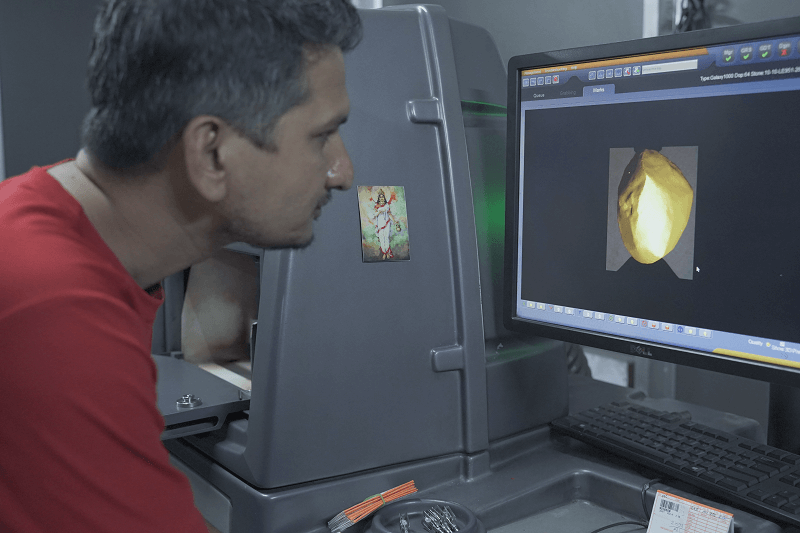
Cleaving or sawing
These are the two methods of splitting the rough diamond into separate pieces that will be further processed as individual finished gems. The main difference between cleaving and sawing is the equipment that is used to split the diamond.
Cleaving was traditionally done with a steel blade and hammer by human hands. In this method, the diamonds are stuck at their weakest planes to cut. Now the same process can be done by machines. A groove is formed on the diamond using laser technology, and then it is struck by a device with the correct pressure to avoid any damage to the diamond, which was very common in the method previously used.
Sawing is a method in which a shape is carved out of a rough diamond without considering planes. Traditionally, this was done with a saw with a diamond-dust-coated blade, and the entire process cannot be done with sawing automated tools or lasers without significant human intervention.There are various kinds of diamond cutting machines now available that use different technologies and methods. Their advanced cutting methods give a more refined shape to the diamonds.
Bruting
After the rough diamond has been reduced to the desired measurements, it needs to be contoured to achieve the basic shape through the process called Bruting. It can be done in 3 ways:
• First, by placing two diamonds and rubbing them in opposite directions
• Second, with laser
• Third, with a disk impregnated with diamond dust
Previously, there were only a few types of cuts that could be pulled out without damaging the diamond. Now, machines can be incorporated for bruting a diamond with precision to achieve any kind of desired diamond cut.
Polishing
This is the process of forming and shaping the facets of the diamond to achieve the perfect angle of reflection and refraction to make the diamond shine and sparkle. This is done in two steps called "blocking" and "brillianteering."
Diamonds in India were traditionally polished on a wooden polishing board by placing one diamond on a swirling arm and one on the board.
In recent times, automated faceting machines have developed to the point where the machines are challenging experienced human polishers for supremacy. They have proven successful in polishing to a very high standard, with reduced weight loss compared to the work of human polishers.

Here’s a list of machines that the Laxmi Diamond team uses:
• Rough Diamond scanning machine (Sarine Galaxy machine)
• Diamond marking machine
• Diamond laser cutting machine/diamond laser sawing machine
• Diamond bruting machine
• Diamond auto polishing machine
• Diamond final polishing machine
• Diamond grading microscopeCVD
• checking machine
• Diamond tension checking machine
• Diamond Florence checking machine
Inspection
Here, the quality of a diamond is examined based on the cut, color, clarity, and carat. This can now be done with the help of compact technologies that scan the diamond and inspect it for its quality within a few seconds

There are various advantages of these technologies, which have led this industry to glory. Some of them are:
• Reduced manufacturing time.
• Precision and quality.
• Negligible human errors.Reduced
• wastage.
Technologies have overtaken every diamond field, from the diamond manufacturing processes to other diamond fields like mining, storing, transporting, selling, sorting, and imaging. The twenty-first century has brought significant change, and we can expect the same from the future that lies ahead, which is undoubtedly bright and shiny.